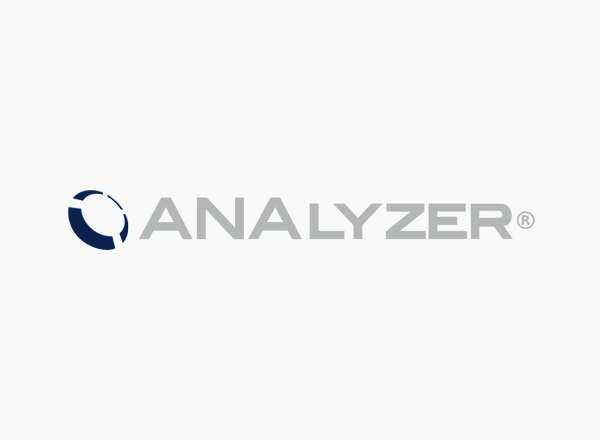
本日は生産技術のT様にお話をうかがっていきます。
よろしくお願いします。
まずはANALYZERを導入する以前の状況などをお聞かせいただけますか?
はい。私が担当している製品は、HV/EV車に搭載されるケースなんですが、もともとは全数全穴を目視検査していました。
でも、目視検査では時間が掛かりすぎるので、人員(工数)削減したいっていうのが1つ。
もう1つは、やっぱり目視検査だと見落としとか、判断ミスがどうしても出てしまうので、機械の力を借りて品質担保を強化しようっていうのが、導入目的でした。
1台につき、検査する穴が60箇所くらいありますし、見落としゼロとなると、検査員は相当神経使いそうですね。
当時の目視検査の時間は、1台何分くらい掛かっていたのですか?
穴以外の検査箇所もあるんですが、トータルで6分以上掛かってましたね。
そのうち穴だけで言うと、何分くらいでしたか?
穴だけだと、3分くらいですね。
残り3分で、他のバリや、端面フライスした部位の鋳巣やキズ・打痕なども検査します。
そうすると、ANALYZERで穴検査に掛かっていた3分が自動化できたのですかね?
そうですね。一部、まだ条件など作り込めてないので、そこは目視でスタートしていますが、その他の穴は自動化できましたし、サイクルタイムも穴だけで言えば2分くらいに短縮できました。
設備でNG判定になったワークはラインの外に出して、1日の最後にそれらのワークの該当箇所だけを目視で再検査します。
それでOKなら良品として流し、NGなら処置するみたいな運用をしてます。
検査機でNG判定になる率が高いと、再検査に時間が掛かりそうですが、そのあたりはいかがですか?
ロットによるバラつきもありますが、NG判定になる率は、本当のNG品と過検出を合わせても、おおむね2~3%くらいで推移してますね。
上手く活用できている前提として、前工程の脱脂洗浄機で、穴の中に油がベトベトに残っているとか無くて、しっかり下処理ができているっていうのが大きいのかなと思います。
ANALYZERを工場に設置して、おおむね1年経過しましたが、現場の方の作業負担は減ってますか?
そうですね。少し前に現場の人と会話した時には、かなり楽になって非常にありがたいですという声は頂いてます。
他にも関連会社の方が見学に来て、設備を見て「これはすごいぞ!」みたいな感じで、とても関心を持ってましたよ。
それは生産技術のT様としても、うれしい反響ですね!
また新しい製品への横展開や、能増などの案件があれば、是非お声掛けください。
今後とも、よろしくお願いします。本日はありがとうございました。