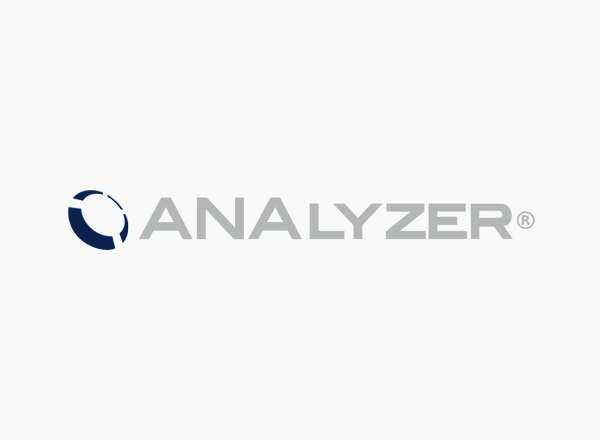
本日は検査ライン導入の責任者であるS様と、現場で調整を担当されているI様のお二人にお話を伺っていきます。
よろしくお願い致します。
こちらこそ、よろしくお願いします。
まずは導入の経緯について教えていただけますか?
はい。順を追って説明しますと、検査の自動化の構想は3~4年ぐらい前からスタートしました。
まずは目視検査をしている箇所をすべて洗い出して、それらが自動検査が可能かベンチマークを行いました。
ベンチマークの結果、費用対効果が見込める箇所を自動化することになり、その検査部位を抽出しました。
それから、今度は機器選定ですね。特に円筒内面の検査は特殊だと思います。
複数のメーカーさんの機器をベンチマークした中で、最終的にANALYZERを選定したという流れになります。
時間をかけて、しっかり準備された事が良く分かりました。ありがとうございます。
当時のベンチマークでは、検査部位(工数)の何パーセントを自動化できそうな見込だったのでしょうか?
弊社が製造している製品は1ワークあたりの穴数が多く、穴検査が全検査時間の約6割を占めていました。なので、特に穴検査は、自動化すると高い効果が見込めそうという判断でしたね。
そうすると、その6割が自動化できたのですね?
そうですね。穴検査でも複数の検査機を使っているので、そのうちのΦ3~M6の径が小さい約20穴をANALYZERで検査しています。
ありがとうございます。
主な穴検査でANALYZERを選定された一番の決め手は何だったのですか?
一番ということならば、機器が非常にコンパクトなことですね。
導入前は設備仕様が決まってなかったので、機器がコンパクトなら、検査機を固定してワークを動かしても良いし、逆に検査機を動かしても良いしというので、使い方に幅があるかなと思いまして。
実際に運用されて、検出能力(精度)についてはいかがですか?
ラインオフの段階では、約1万台のワークを流して、NG品の見逃しはゼロ。過検知が3台(穴)という結果でした。
過検知率は0.03%(穴数で換算すると0.0015%)ですね。
はい。過検知については、導入前のトライで、ロットによる素材の影響で、素材面の黒ずみが問題になりそうという懸念があったので、もう少し精度を上げたいなというので、追加でAI判定機能(DEEP-EYE)を投入しました。設定はI君が対応しています。
特にΦ4.2mmの3か所の穴で過検知が出やすいので、私が勉強がてらDEEP-EYEで過検知の画像を抽出して、OK側へ救済できるように設定して活用しています。
DEEP-EYEを設定してから、その3か所の穴も、ほぼ過検知が出てないですね。
出来れば他の穴にも横展開したいなと思ってるんですが、前工程でしっかり洗浄できているおかげで、実際の切粉NGがほぼ発生しないので、学習させるデータがなくて、いったん現状維持で流動しています。
しっかりDEEP-EYE(AI)の効果が出ていて、私たちも嬉しいです。
今のところ順調に推移しているような印象ですが、ANALYZERを導入する前と後で、思っていたのと違ったとか困ったなということはありましたか?
・・・(お二人、しばし沈黙)
過検知も、あまり出ず。なので導入当初は、パラメタをほとんど触ることもなく、深刻なことはなかったと思います。
アカデミーでレクチャーを受けてから、何となく触ってみるようになったんですが、最初は具体的な設定方法が分からなかったんで、都度、御社に連絡して設定のサポートをお願いしてっていう。
まあ、いい意味というか、思ってなかったというと失礼なんですけど、検査機の導入が初めてという事もあって、御社の手厚いサポート体制は、非常に心強いと感じています。ラインを敷くにあたって、他にも何社か関わっていただいていますが、本当にサポート体制は抜群だと思います。
サポート体制を高く評価していただき、大変ありがとうございます。
これからもコストに見合った製品とサービスを提供できるように頑張ります。
本日はお忙しい中、ありがとうございました。