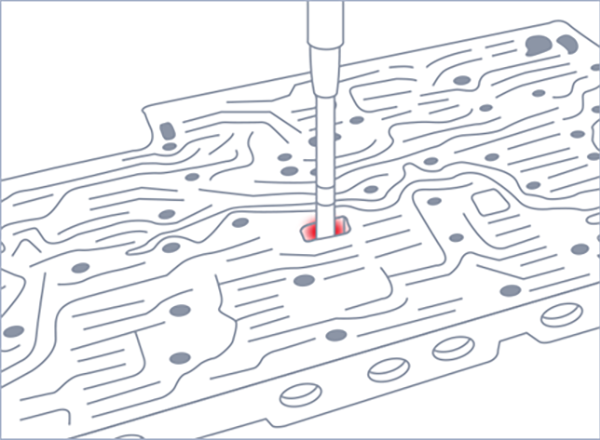
まずはANALYZERを知った経緯などお聞かせいただけますか?
当時のGMが貴社のパンフレットを見て、興味をもったのがキッカケです。ちょうど部門のテーマとして「検査の自働化」が挙がっていたので、タイミングも良かったのもあります。
その後は、どんなアクションでしたか?
シグマさんにサンプルを送ってトライをお願いして、見たい欠陥がちゃんと見れそうだなと判断できまして、タイミングも良く導入を決めた後に、ANALYZERを使っている系列工場に見学に行かせてもらいました。その実績も、採用の自信になったと思います。
系列工場では10年以上前から数ラインでご使用いただいています。工場見学は、どんな点が参考になりましたか?
ANALYZERはレーザを使いますので、設備化の安全仕様とか、ワークをハンドリングするマシニング機構、あとは見逃し率・過検出率といった判定精度の実力を参考にさせてもらいました。
実際、自社工場に導入されていかがでしょう?
系列工場でも見たとおり、穴の検査に関する信頼性は十分あると思います。導入からいろいろと前工程の改善を行っている途中で、まだ弊社が目標としている過検出率には達していませんが、AI判定のトライアルなども含め、こちらの質問や相談にタイムリーにレスポンスをもらえて、ある程度見込みが立ってきました。そういう意味では納入後のサポートも手厚いと感じています。
ご評価いただき、ありがとうございます。前工程の改善途中ということは、けっこう毎日設備の前に貼り付いている感じですか?
いえ、通常はオペレータ1人で回しています。私は変化点が発生したり、異常が多い時に現場に行って調査・調整をしています。
それ以外に課題と思われることはどうでしょう?
サイクルタイムと価格ですかね。ワークを6軸ロボットで検査機内に搬入出できるように半年前に改造をしたのですが、もう少し1台あたりの検査時間を短くしたいです。
あとは導入価格ですね。弊社では省人化に関する設備投資は、オペレータ1人=2年で回収が基本的な考え方になっています。今回は穴の中に特化というか、そこは人では検査が難しいので採用に至ったわけですが、「面(外観)」の検査も何らかの手段で自動化しないと省人化につながりにくいので、それらをトータルで考えると比率的にもう少し価格が下がると導入しやすいかなと思います。
貴重なご意見ありがとうございました。より使い勝手を高めて行く事を検討させて頂きます。今後ともどうぞよろしくお願いします。