Client We will introduce the customers who have brought our product
Product information We will guide you through products that boast overwhelming performance
Main products
ANALYZER3 Φ6
Estimate inspectable inner diameter:Φ7mm~Φ30mm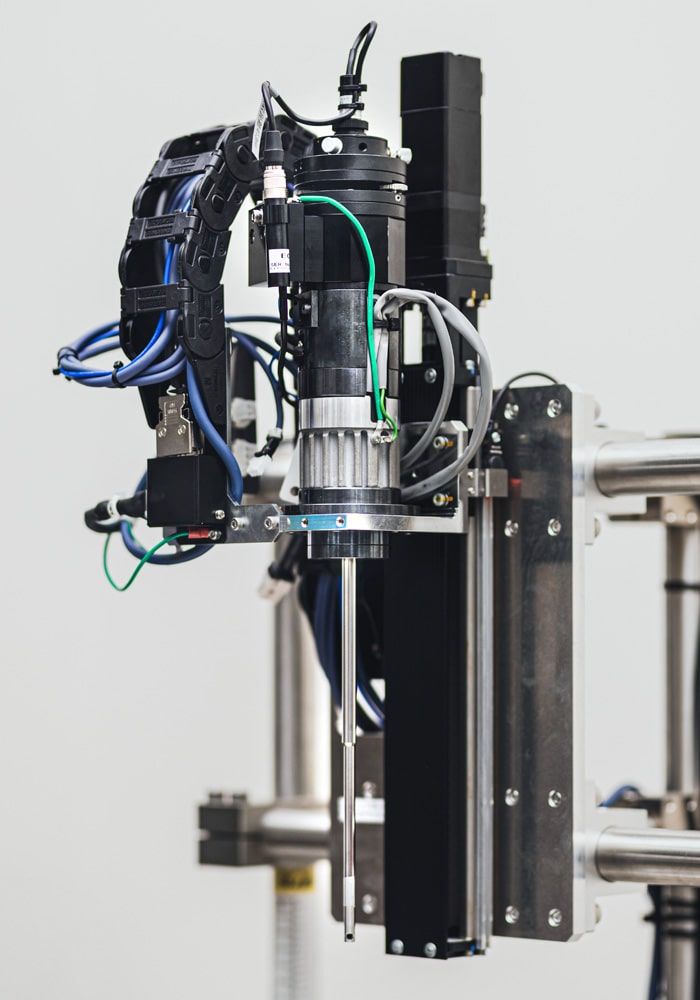
ANALYZER3 Φ6
Estimate inspectable inner diameter:Φ7mm~Φ30mmThis is a stand model for inspecting bore with the inner diamter of Φ7mm or more
Problem solving
- Labor costs can be reduced.
- As it is a numerical standard, the quality is stable.
- It is possible to prevent excessive NG products due to excessive quality.
- Work efficiency can be improved by overwhelmingly shortening the inspection time.
Product specification
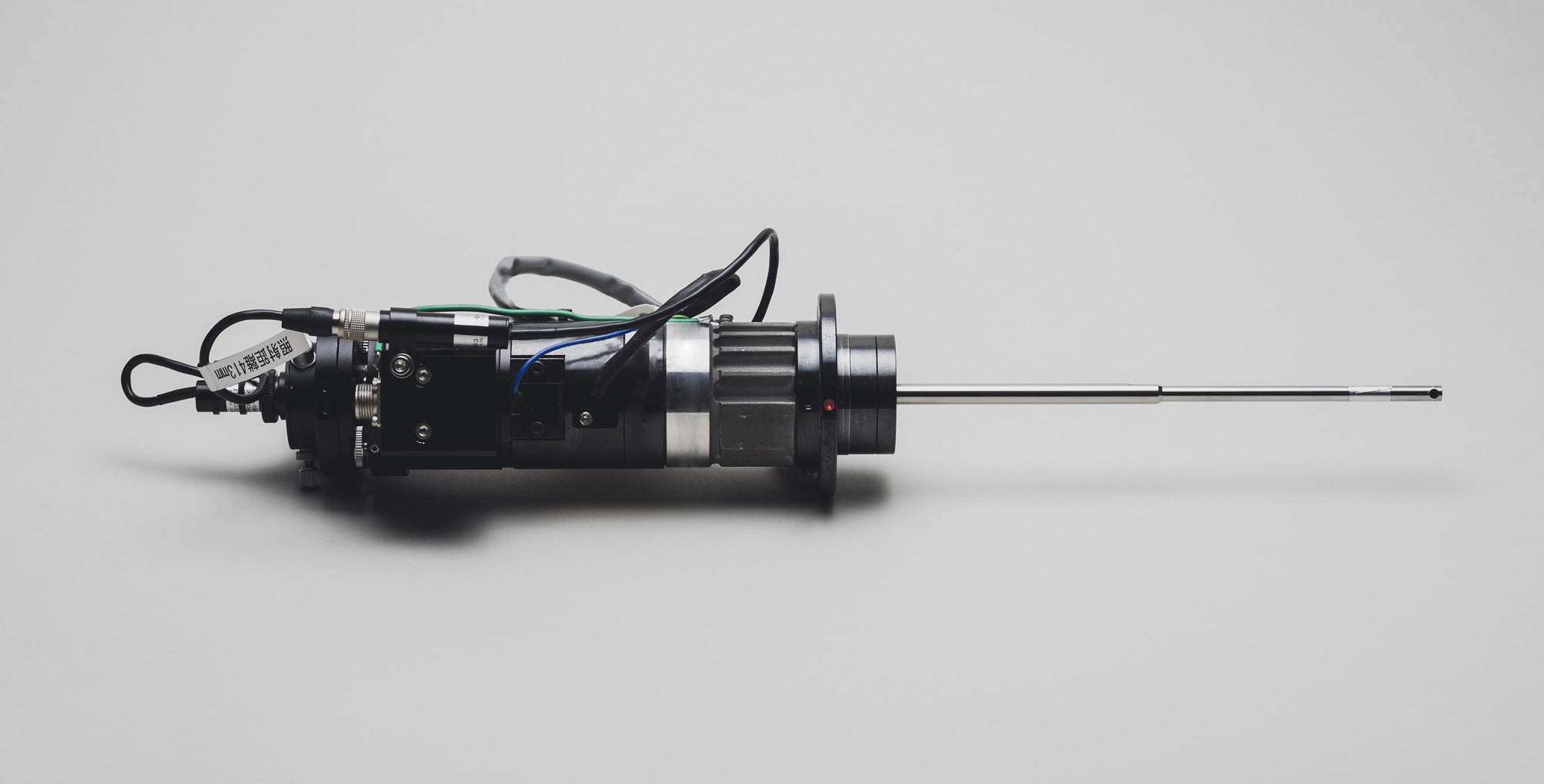
Device specification
Model | SG-LSDC-6-203-15K-STD |
---|---|
Method | Optical scanning method |
Light source | Red semiconductor laser (wavelength 640nm, maximum 40mW) |
Laser class | Class 3B |
Detection component | Direct light |
Target bore | Φ7mm~ |
Rotation speed | 15,000rpm |
Measurement length availability | 200mm |
Minimum detectable size | 0.2mm |
Estimate inspection speed | About 4sec ※In the case of Measurement length 100mm, Resolution 0.1mm |
Sampling frequency | ~2,400kHz |
Power | 100、200V |
Schematic drawing
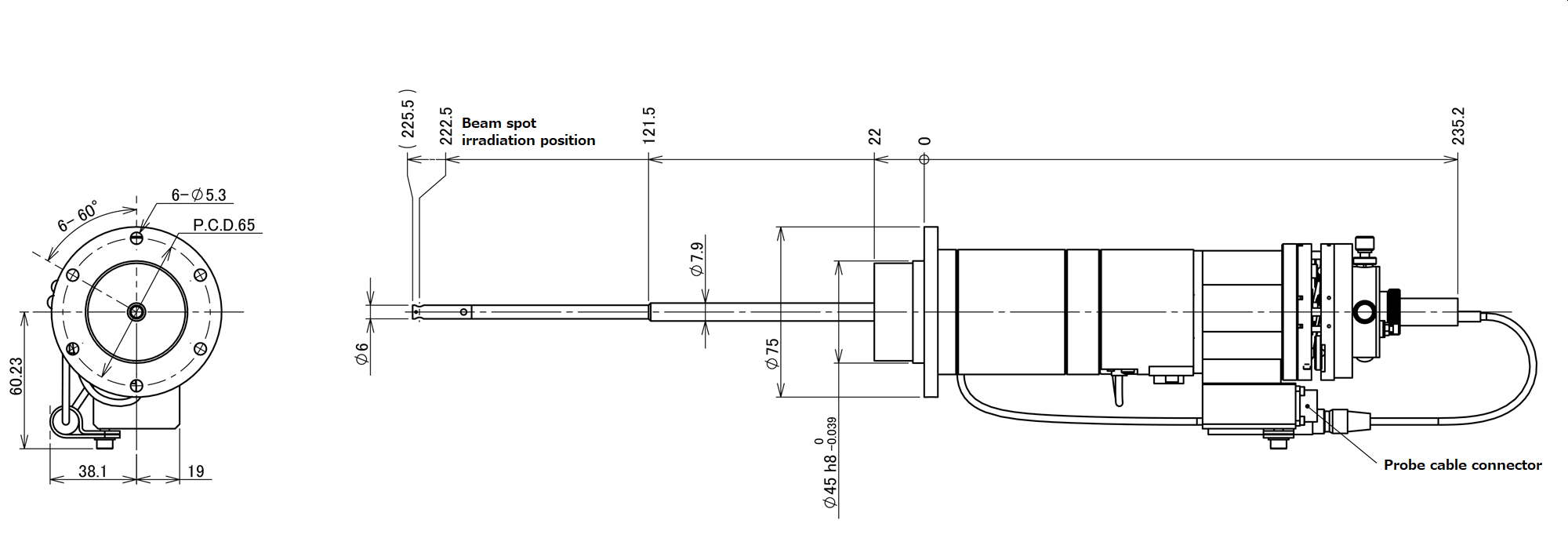
List of other products

Product name | Model | Target bore | Rotation speed | Measurement length availability | Minimum detectable size | ||
---|---|---|---|---|---|---|---|
|
SG-LSDC-6-203-15K-STD | Φ4mm〜 | 10,000rpm | 50mm | 0.2mm | ||
|
SG-LSDC-8-190-15K-STD | Φ9mm〜 | 15,000rpm | 190mm | 0.2mm | ||
|
SG-LSDC-6-203-18K-NEO | Φ7mm〜 | 18,000rpm | 200mm | 0.2mm | ||
|
SG-LSDC-6-203 | Φ7mm〜 | 15,000rpm | 200mm | 0.2mm | ||
|
SG-HDRM5 | Φ7mm〜 | 15,000rpm | 200mm | 0.2mm |
Product summary
Product features
- Inspection is possible with non-destructive and non-contact.
- Can inspect areas that cannot be visually inspected
- OK / NG judgment can be automated by setting the defect judgment criteria.
- The work is irradiated with a laser and the reflected light is captured. So the influence of ambient light is small.
- Inspection data will be saved with defect information, so feedback on the manufacturing process can be done
Merit of using the product
Inspection costs can be reduced.
Prevent the outflow of defective products.
Improves traceability.
Individual differences in inspection quality can be eliminated.
System configuration
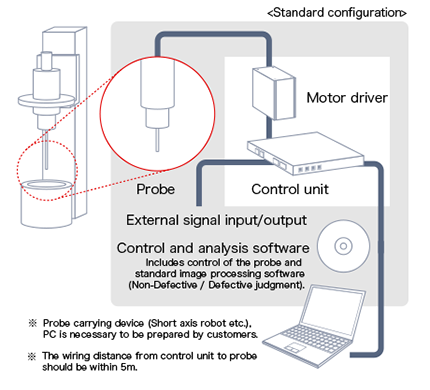
Working principle
STEP1
It irradiates a laser beam and scans the entire surface to be inspected.
STEP2
Utilizing the fact that the angle of light generated from scratches and defects differs greatly between direct light and diffracted light, the amount of reflected light is separated and received.
STEP3
It analyzes changes in the amount of light with a unique algorithm and automatically determines blowhole, scratches, cracks, etc.
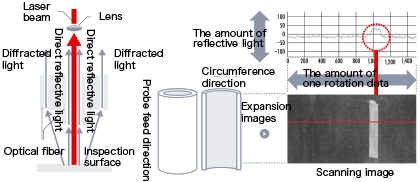
Introduction example We have introduced more than 450 units from 75 companies, mainly in the automobile industry.
Valve body blowhole inspection
The valve body is a part used in automatic cars. It is the heart that controls the shift. If this part gets defected, heavy shift shock may occur. The valve body has multiple holes with different diameters, and this device inspects the wall surface of the holes to check defects.
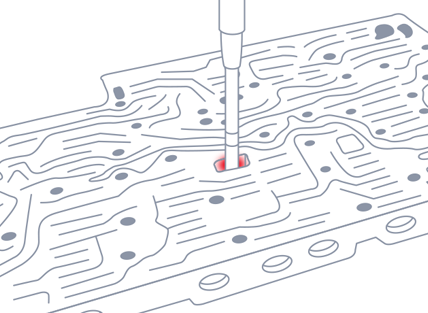
Inspection procedure
- Set the work in the device.
- Center the probe and workpiece at the machining center.
- Inspect the inner wall and make an OK / NG judgment.
- Repeat steps 2 and 3 with multiple holes to make the final judgment.
- Work will be discharged
Usage environment, etc.
Device installation location | In the factory line |
---|---|
Probe used | Probe rotation type SG-LSDC-6-203 |
Main inspection | Blowhole, scratches, cracks, dents, etc. |
Inspection target diameter / measurement length | Φ8~15mm L=40~80mm |
Takt time | About 10sec(10holes inspection) |
Engine block blowhole inspection
It is used to inspect the main parts of car engines.
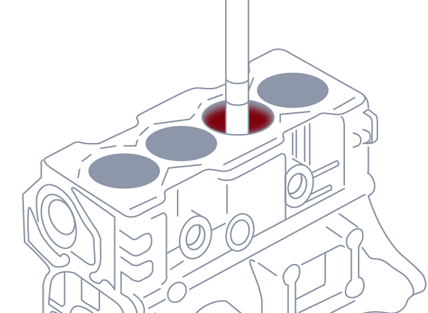
Inspection procedure
- Work is transported by a belt conveyor.
- Decide the work position in the stage and lift up.
- Inspect the inner wall and make an OK / NG judgment.
- OK products will go to the subsequent process,NG products will be re-inspected visually.
Usage environment, etc.
Device installation location | In the factory line |
---|---|
Probe used | Probe rotation type SG-LSDC-8-190 |
Main inspection | Blowhole, scratches, cracks, dents, etc. |
Inspection target diameter / measurement length | Φ80mm L=120mm |
Takt time | About 40sec(4holes inspection) |
Sleeve blowhole inspection
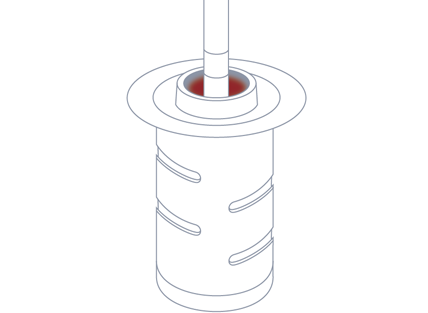
Inspection procedure
- Transport the work in the index table.
- Inspect the inner wall and make an OK / NG judgment.
- OK products will go to the subsequent process, NG products will be discharged by each defect type.
Usage environment, etc.
Device installation location | In the factory line |
---|---|
Probe used | Probe rotation type SG-LSDC-6-203 |
Main inspection | Blowhole, scratches, cracks, dents, etc. |
Inspection target diameter / measurement length | Φ12mm L=65mm |
Takt time | About 5sec/work |
Inspection of screw holes in the differential case
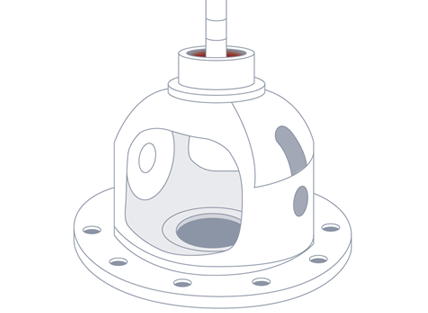
Inspection procedure
- Person sets the work by hand and push the start lever.
- The inspection starts as soon as the shutter closes.
- Inspect 12 screw holes while turning the workpiece on the index table.
Usage environment, etc.
Device installation location | In the factory line |
---|---|
Probe used | Probe rotation type SG-LSDC-6-203 |
Main inspection | Blowhole |
Inspection target diameter / measurement length | M11mm L=20mm |
Takt time | About 45sec(12 screw holes inspection) |
Impeller scratch inspection
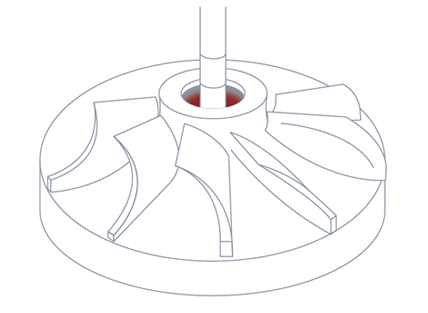
Inspection procedure
- Set the work on the station with a 6-axis robot.
- The inner diameter of the shaft hole of the impeller is inspected to determine OK / NG.
- OK products will go to the subsequent process,NG products will be re-inspected visually.
Usage environment, etc.
Device installation location | In the factory line |
---|---|
Probe used | Probe rotation type SG-LSDC-2.3-50 |
Main inspection | Scratch |
Inspection target diameter / measurement length | Φ5mm L=60mm |
Takt time | About 15sec/work |
Bearing roughness residue inspection
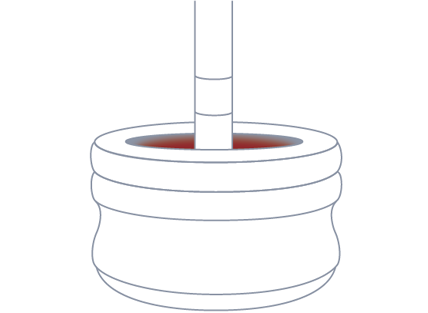
Inspection procedure
- Transport the work in the index table.
- The inner(outer) diameter is inspected and determine OK / NG.
- OK products will go to the subsequent process,NG products will be re-inspected visually.
Usage environment, etc.
Device installation location | In the factory line |
---|---|
Probe used |
|
Main inspection | Roughness residue |
Inspection target diameter / measurement length | Φ30mm L=15mm |
Takt time | About 4sec |
Rocker arm pins scratch inspection
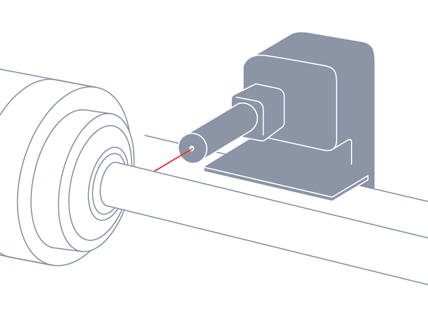
Inspection procedure
- The work is put into the rail from the parts feeder and rolled by the weight of the work.
- Stop the work at the inspection position, clamp both ends of the work, and rotate the work at high speed.
- Inspect the outer wall and make an OK / NG judgment.
- OK products will go to the subsequent process,NG products will be re-inspected visually.
Usage environment, etc.
Device installation location | In the factory line |
---|---|
Probe used | Probe rotation type SG-LSGD |
Main inspection | Scratches, dents, rust, etc. |
Inspection target diameter / measurement length | Φ10mm L=10mm |
Takt time | About 3sec |
Inspection of screw holes
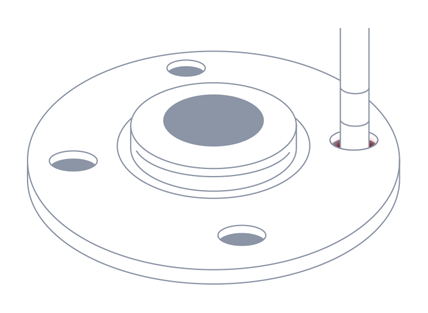
Inspection procedure
- Transport the work in the index table.
- Inspect 4 screw holes and judge whether each hole is OK / NG.
- OK products will go to the subsequent process,NG products will be re-inspected visually.
Usage environment, etc.
Device installation location | In the factory line |
---|---|
Probe used | Probe rotation type SG-LSDC-2.3-50 |
Main inspection | Contamination, screw pitch, etc. |
Inspection target diameter / measurement length | M6mm L=10mm |
Takt time | About 10sec(4 work inspection) |
Flow until the start of operation We will guide you through the basic flow from inquiries to the start of operation.
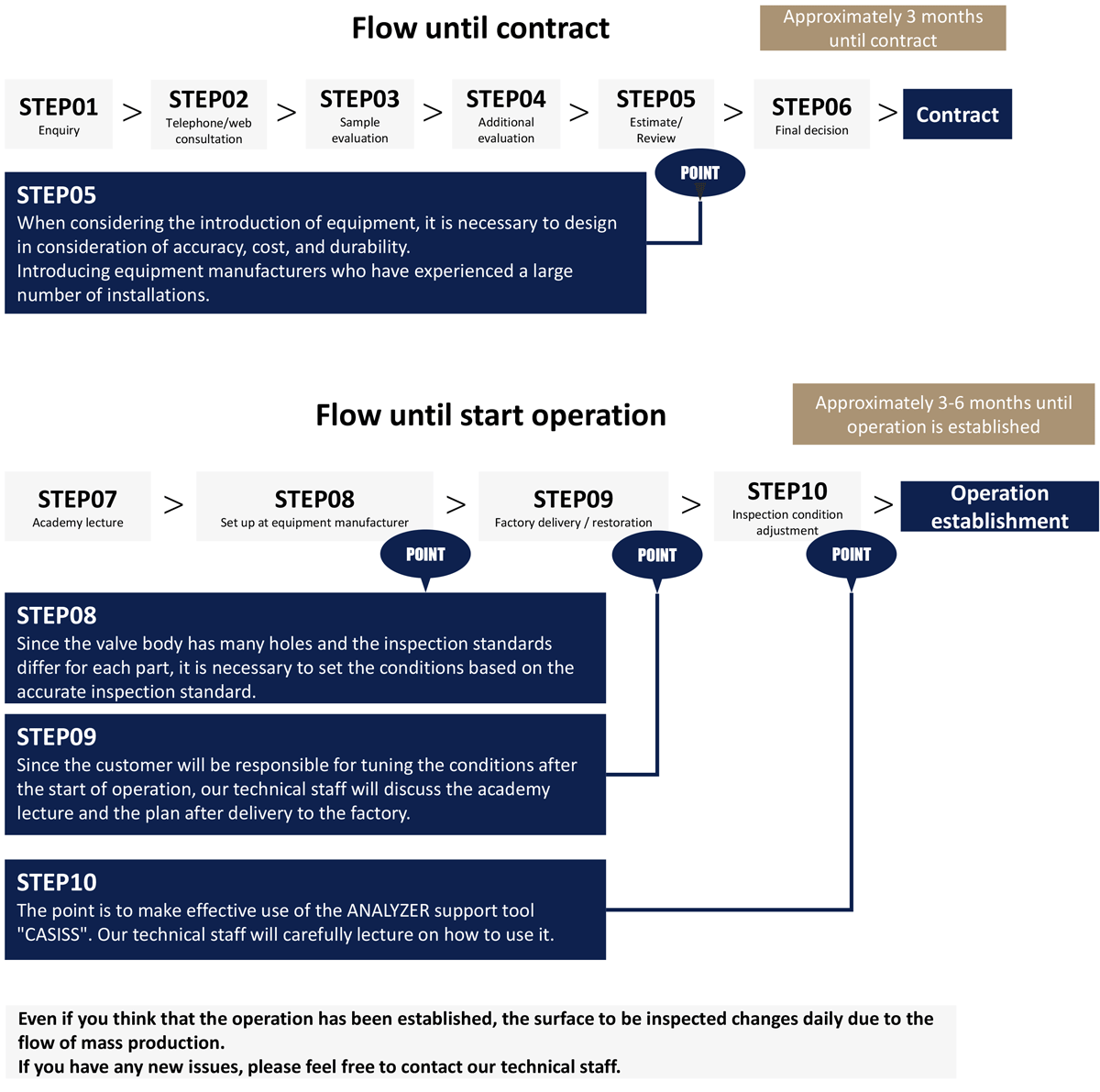
Company information We will guide you about ANALYZER Inc.
Mission
The original laser technology frees the operator from heavy inspection work, and the DX technology revolutionizes the manufacturing of mass production sites.
Vision
Continue to challenge the unknown, promote reduction of environmental load in mass production process, and contribute to SDGs.
※Reduction of loss due to excessive quality / Prediction and suppression of defects / Manufacturing of fuel-efficient parts
Company summary
Trade name | ANALYZER Inc. |
---|---|
Location address | 3-13-60-11, Kagamiyama, Higashi hiroshima, Hiroshima, 〒739-0046 Japan |
TEL | +81(82)-426-6672+81(82)-426-6672 |